POLYETHYLENE
For the manufacture of film and bags, there are two main types of polyethylene: Low Density Polyethylene (LDPE) and High Density Polyethylene (HDPE), also known as Low Pressure Polyethylene (LPPE), although a wide range of grades is available for each. The processes used to obtain both types are different, and their physical and chemical properties also differ significantly, as a result of their distinct molecular structure.
Low Density Polyethylene is obtained at high pressures (between 1,000 and 3,000 atm.) and at temperatures between 100 and 300°C in the presence of oxygen as a catalyst. It is a soft and elastic thermoplastic product with a density of 0.92. In its natural state, the film is completely transparent, although this characteristic decreases depending on the thickness (gauge) and grade.
High-density (low-pressure) polyethylene differs from the former in that it is obtained at lower pressures and temperatures, in the presence of an organometallic catalyst. Its characteristics include greater hardness and rigidity. Its density is higher (0.94). In its natural state, the film, while translucent, is not completely transparent, taking on a waxy appearance. Like the former, its appearance will vary depending on the grade and thickness (gauge).
By adding appropriate colorants, polyethylene films can be obtained in a wide variety of colors.
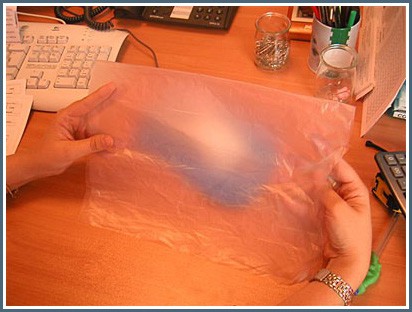
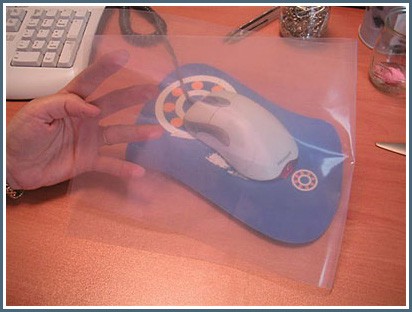
POLYPROPYLENE
There are basically two types: Monooriented or Cast (for bag manufacturing and complexes with other plastics) and Bioriented (usually used in film for use in automatic packaging machinery, and also for complexes).
Polypropylenes (PP) are characterized, unlike the previous ones, by their greater transparency and more crystalline appearance. Their mechanical characteristics are quite distinct, and their density is 0.90.
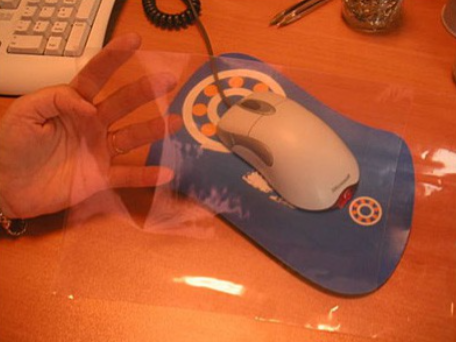
TABLE OF PROPERTIES
LDPE | HDPE | PP | ||
Density | 0.92 | 0.94 | 0.90 | cm³/g |
Weight/Grammage | 23 | 23.5 | 22.5 | g/m², film of 0.025 mm (gauge 100**) |
Breaking Load | 100-170 | 210-380 | 300-400 | Kg/cm² |
Elongation at Break | 500-725 | 100-200 | 500-700 | % |
Hardness | 40-45 | 60-70 | 85-95 | (SHORE) |
Thermal Conductivity | 8 | 11-13 | 3.3 | 10 (4th) cal/s cm. ºC |
Specific Heat | 0.55 | 0.55 | 0.44 | kcal/kgºC |
Softening Temperature | 80-90 | 90-120 | 140-160 | (VICAT)ºC |
Melting Temperature | 110-115 | 130-140 | 170-175 | ºC |
* Table for comparative purposes between materials. Standardized tests performed with specific material grades and conditions.
** GAUGE: To describe the thickness of the aforementioned materials, we often refer to microns or gauges. A micron is one thousandth of a millimeter, that is, 1 millimeter divided into 1,000 parts. The gauge is the thickness in microns multiplied by 4. Thus, as an example, a polyethylene film with a thickness of 25 microns is Gauge 100.
To measure the thickness of materials, a precision device called a PALMER or micrometer should be used; the typical caliper is also commonly used.
ECONOMY/SOCIETY/ENVIRONMENT
Polyethylene and polypropylene are noble, recyclable, and non-polluting materials; their combustion does not produce gases harmful to the atmosphere. Products made from these materials, when handled properly, are suitable for food use.
Their easy processability, low cost, excellent balance of physical properties, and low density are the reasons for their use in numerous applications, to the point that it would be impossible for us to do without all the products made from these materials in our daily lives.
Their impermeability, transparency, and, above all, their great resistance compared to the small volume they occupy, make containers and packaging made from these materials good allies for the environment, since one of the biggest problems we face in society is the large quantity and volume (m3, kg, etc.) of waste (garbage) generated.